The rise of electric vehicles is creating many new material opportunities. One such material class is the die attach material used in power electronics. Here, the trend towards higher power densities and thus higher operating temperatures is opening up the market to new non-solder solution despite the substantially higher costs of the alternatives.
[dropcap]T[/dropcap]he IDTechEx report, “Die Attach Materials for Power Electronics in Electric Vehicles 2020-2030”, finds that metal sintering including all Ag and Cu types will become $30M market by 2026 in electric vehicle power electronics. This article offers a review of this growing market trend.
Growth in addressable market
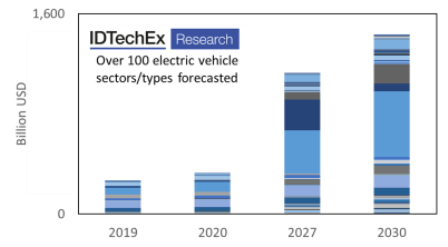
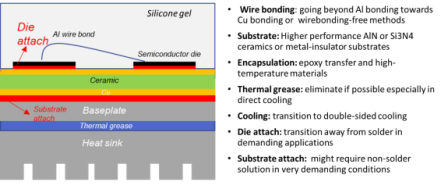
Naturally electrification of mobility expands the power electronics market. In an electric vehicle, power electronics fulfil various functions including on-board charger, various HV-LV DC-DC converters, and the main traction motor inverter. The performance requirements across these functions differ.
Yet, some common technology trends cut across all of them. In particular, the operating temperature and frequency of power electronics is rising with profound consequences across device and material technology development and choices. The emerging generational shift towards SiC MOSFETs and GaN HEMTs partially underpins and certainly accelerates these long-term trends.
Market drivers and alternative options
The image below shows a traditional power module package. It outlines how and why many materials and designs will need to change to enable and sustain the trend towards higher power densities and junction temperatures. Today, the temperature is typically around 120-150C and is already approaching 175C in some cases. It will soon go higher, potentially approaching 200C or higher in the future.
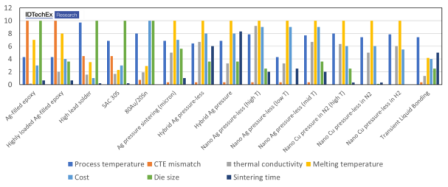
This article and the associated study “Die Attach Materials for Power Electronics in Electric Vehicles 2020-2030” are concerned with die and substrate attach technologies. Today, solutions such as SAC solder are commonplace. The rise in operating temperature, as well as the need to prolong product lifetime under even harsher thermal cycles pushes the requirements beyond what solders – especially lead-free ones – can achieve. As such, alternatives are needed. This need will only grow in the future. The IDTechEx report offers a detailed assessment of all existing and die attach technologies, examines the market trends driving the need towards alternatives, reviews all solder alternative technologies and solders, analyses all modules and module makers who have demonstrated solder alternatives, and develop quantitative realistic market forecasts segmenting the market electric vehicle type, power electronic function, and material such as solder, micro-sized Ag metal sintering, nano/hybrid metal sintering, Cu sintering, and TBL.
Trends in metal sintering
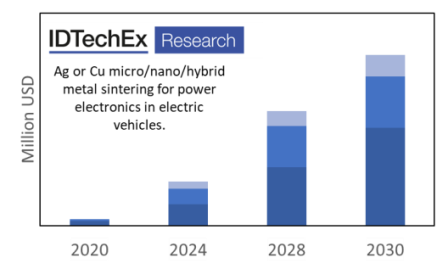
Metal sintering is one such alternative. The technology has been in development mode for over a decade. It is already commercialized in applications such as renewables and also in leading electric vehicles. Here, metal particles are sintered with or without pressure to form a near solid-like thin film, offering high joint shear strength, high thermal conductivity (150-300 W/mK), and a very high bulk-like melting temperature (962C) resulting in a high homologous temperature.
Traditionally, micro-sized silver particles and pressure sintering have been used. Here, the paste is typically stencil or screen printed. It is then dried, e.g., 60-120C for 5-15min. Next, it is sintered on a head substrate, e.g., 130C, using a pressure (e.g., 30MPa @ 200-250C) for a few minutes (e.g., 3-5min). This pressure sintering technology is the most mature, is able to support the largest die areas, and offers the highest shear strength. It, however, requires additional equipment, and can not easily support uneven module topographies and/or ultra-thin dies.
Many are now developing varieties that enable pressure-free sintering and/or are reducing the sintering pressure or temperature. Typically, pressure-free sintering takes too long, e.g., 200min. It also only supports small die areas, e.g., 24 mm2. Companies are now offering silver nano and/or hybrid pastes able to at least partially alleviate these performance shortcomings. Suppliers of such products are multiplying, and some have already found their way into the market. To learn more about all the technologies and all the players including all players offering nano or hybrid sintering pastes please see the IDTechEx report “Die Attach Materials for Power Electronics in Electric Vehicles 2020-2030”.
In parallel, companies are sampling copper-based metal sintering pastes. This work is motivated by (a) the lower cost of raw copper, and (b) the potential lack of CTE mismatch between copper joins and copper clads. Despite these appeals, there remain some hurdles. Some solutions require a metallization gas. Typically, hydrogen is used to speed up the process especially in pressure-less sintering. Otherwise, normally N2 is used during pressure sintering. In any case, additional equipment and process know-how is required. As ever, oxidization prevention and long-term reliability remain concerns. New semi-commercial Cu offerings are now close to addressing both these concerns. To learn more about technology, readiness level, costs, suppliers, and market adoption of Cu and TBL as well as Ag based metal sintering alternatives please see “Die Attach Materials for Power Electronics in Electric Vehicles 2020-2030”.
Market adoption and growth
IDTechEx have developed a detailed market study. Our work forecasts the market in value, mass/volume, and demand area. Our model considers the evolution of die area resulting from the emergence of wide-band-gap devices. These enable higher power densities, thus shrinking device area for a given power level and/or reducing number of device elements often deployed to spread the current. Furthermore, our model builds on our 15 years of ongoing research in electric vehicle markets, which gives us access to granular and up-to-date market figures concerning all aspects of the great electric vehicle market (not just passenger cars). Building on our market knowledge, player insight, and technology understanding, IDTechEx segment our total addressable market forecasts by material type, electric vehicle type, and power electronic function. The materials covered therein include solder such as SAC, non-nano Ag sintering, nano/hybrid silver sintering, Cu sintering, and transient bonding liquid (TBL).
As shown below, IDTechEx find this to be an exciting market. The market suppliers who pioneered the development are now reaping the benefits. They remain ahead in terms of optimized compositions and future developments including product form factor (beyond paste). Many paste markets are now fast playing catch up. Overall, IDTechEx find the market for all types of metal sintering combined will exceed $30M by 2026. The IDTechEx report offers market forecasts – in value and mass – segmented by electric vehicle type, power module function, and die attach material including solder and SAC, LTB, nano-Ag, non-nano Ag, and Cu sintering.
To connect with others on this topic, join us at The IDTechEx Show! Europe 2020, 13 – 14 May, Estrel Convention Center, Berlin, Germany. Presenting the latest emerging technologies at one event, with six concurrent conferences and a single exhibition covering 3D Printing and 3D Electronics, Electric Vehicle Materials, Graphene and 2D Materials, Printed and Flexible Electronics, Sensors and Wearable Technology.