“In Nigeria then, Volkswagen Beetle, for instance, was assembled from CKD (Completely Knocked Down) kits. Local contents of over 20% were added. Volkswagen Beetle was then in Nigeria, the People’s car, as it sold for as low as N2,500 per unit…”
Since 1950, the Volkswagen Passenger Cars brand has been exporting vehicles dismantled into individual parts in order to assemble them in the destination country. One of such destination countries used to be Nigeria from 1970s to early 90s.
In Nigeria then, Volkswagen Beetle, for instance, was assembled from CKD (Completely Knocked Down) kits. Local contents of over 20% were added. Volkswagen Beetle was then in Nigeria, the People’s car, as it sold for as low as N2,500 per unit. This happened until the Nigerian automobile industry suffered a policy summersault and the Volkswagen plant shut down.
The plant was later acquired by Stallion Group and converted to multi-brand assembly plant. The plant has been revived in the country. But unfortunately, it has gone back to rolling out vehicles made from Semi Knocked Down (SKD) Kits.
For Volkswagen Group worldwide, CKD approach was to open up new markets. Nowadays, CKD also ensures supplies to Volkswagen’s global production network – and is a key factor in sales.
To date, about 200 million vehicles have been exported to countries throughout the world. About 3 million further vehicles or parts are added every year. The first vehicle to be assembled from individual parts supplied in a box was the legendary Beetle.
The CKD approach may be adopted for a number of reasons; it may not be viable to build a factory in the country concerned. Volumes may be too low for local production. The cost of new tooling for a local plant may be too high or customs and import regulations may call for this approach.
Wolfsburg is the nerve center
This is how it works: all the orders received from overseas plants are collected centrally in Wolfsburg. The supply management team ensures that the vehicle parts are available from the European plants and suppliers.
The parts are then bundled and packaged at one of the eight distribution centers, loaded into containers and shipped by sea, rail or air to overseas countries and Russia, where they are assembled. At the distribution centers in Wolfsburg, Salzgitter and Kassel alone, a total of 660 employees work in this area.
Other locations are Duisburg, Emden, Fallersleben, Wilhelmshaven and Martorell (Spain). These eight packaging centers ship a total of about 1.7 million cubic meters of goods every year, corresponding to about 25,000 overseas containers.
From the receipt of an order, it takes about eight weeks before the vehicle is delivered in the destination country. All in all, about 90 different vehicle projects of overseas plants are supplied via CKD from Europe.
First the Beetle then the box
Everything started in 1950, when the first Beetle dismantled into individual parts arrived in Ireland. This was followed by deliveries to South Africa, Argentina, Brazil and Mexico. Especially in South America, the assembly of CKD vehicles laid the foundation for the major production companies now operating there, such as Volkswagen do Brasil or Volkswagen de México.
Nowadays, there are 27 assembly locations in 10 countries. The largest CKD assembly plant is located in South Africa; for example, the Polo for all right-hand-drive markets is assembled there. Another export bestseller is the Tiguan, which is also built from CKD kits in Russia and Mexico. Further plants are located in the USA, China, Brazil, Argentina, India, Malaysia and Indonesia.
From hand-packed to high-tech
Once, the parts were packed in boxes manually. Nowadays, high-tech systems are used. Highly advanced robotic systems provide support for loading the components at the distribution centers. They are equipped with a special hand attachment allowing them to grip vehicle parts of all shapes and sizes. This relieves the burden on the team, especially when packing heavy vehicle parts.
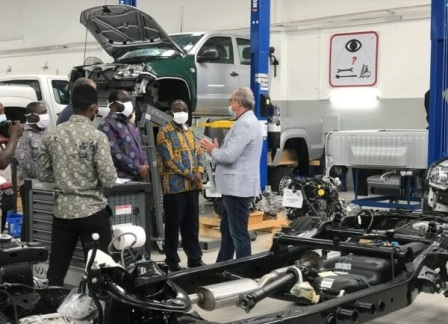
Bots using artificial intelligence also simplify email communications with suppliers. They read the emails and react independently. For example, if a supplier responding to an enquiry indicates that a batch will be delivered in several consignments, this information is automatically detected by natural language processing (NLP) and directly transmitted to the SAP production management system.
Commenting, Burkhard Hüsken, Head of CKD of the Volkswagen Passenger Cars brand said: “We used to need only one or two faxes per week for coordination with the overseas plants.
“Nowadays, we work with our production plants on a real-time basis and manage about 9,000 part numbers for worldwide shipment. The tasks of our employees have changed fundamentally. They are no longer simply box packers but are now logistics data experts.”
©Copyright MOTORING WORLD INTERNATIONAL.
All rights reserved. Materials, photographs, illustrations and other digital content on this website, may not be reproduced, published, broadcast, rewritten or redistributed in whole or in part without prior written permission from Motoring World International
Contact: [email protected]